KCMC co., ltd
Korean Coating Materials and Components
About Process Materials, Inc.
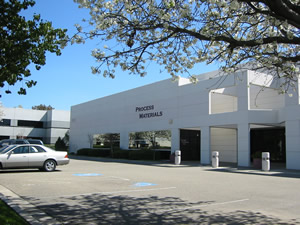
Process Materials has become a leading provider of materials by supplying customers with superior quality and consistency-targets known for dependability. Our customers know they will receive targets produced to their exact specifications, delivered on time.
Founded in 1998, Process Materials has earned a global reputation for its commitment to quality and service where trust is as important as technical knowledge.
A Global Committment to Quality & Service
Materials

Process Materials offers a broad range of purities to satisfy the diverse range of semiconductor to industrial applications.
Manufacturing
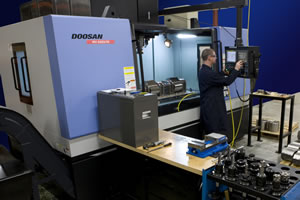
Targets are machined on an automated CNC-controlled process system to maintain the dimensional stability and surface quality of the material. This process is controlled by a statistical measurement system. Our target production facilities are designed for maximum flexibility to assure that products conform to the exact specifications of every customer.
Quality Assurance
Raw materials enter a dedicated receiving area where they are verified for conformance to purchasing specifications prior to preparation. At this point, they are prepared for the appropriate manufacturing process. Process Materials produces every order with proven techniques, flexible capabilities and the finest fabrication, measuring and testing equipment.Analysis of materials include glow discharge mass spectrometer (GDMS) testing for trace elements, atomic absorption testing for major contaminates within the metal and c-scan testing for bond integrity. All targets are engraved with a lot number that is fully traceable to the original melt/source.
Cleaning, Packaging & Documentation
All materials are cleaned and packaged to customer specifications in a CFC-free, class 100 clean room. Products are heat-sealed and vacuum/back filled with an inert gas. All product shipments include a Certificate of Analysis and Material Safety Data Sheet.Materials are produced to our standard specifications unless directed otherwise by the customer.
Backing Plates
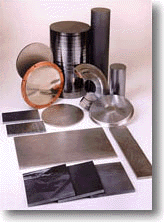
Rotatable Backing Tubes
Sputtering Target Bonding Services
Process Materials implements a proprietary technique to metallic bond sputtering targets and backing plates. Our bonding process ensures the thermal integrity of the interface between the system's cooling assembly and the surface of the target, which experiences the most heat. The bonding of the sputtering target to a backing plate is a very critical procedure. Process performance and process stability are highly dependent on a good bond. Custom fixtures and gauges are used to provide precise control of solder layer thickness and target/backing plate alignment, securing a high integrity bond.
Backside Metallization
Process Materials sputter deposits backside metallization layers on targets before bonding. This metallization accomplishes the following:
Bonding/Solder Material
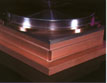
Tolerances
Process materials procedures allow all geometric tolerances to be maintained at very close limits. The parallelism of the targets and the thickness of the bonding layers are tightly controlled. All incoming customer backing plates are inspected and measured prior to bonding.
Bond Integrity
The most critical area of the bond is the periphery, the bond seam. Even the smallest void or an oxide layer may cause severe process instabilities. Each target seam is inspected to guarantee shape, continuity and integrity of the region. Process Materials guarantees that, on average, at least 97% of the target area is solidly bonded.
Quality
Whether you use the most common backing plate material, OFHC copper, molybdenum, stainless steel or aluminum, Process Materials quality bonding techniques eliminates cavities at the edges of a solder bond that may entrap air and form a virtual vacuum leak in your sputtering system. We make every effort to prevent bond flaws that might degrade the base pressure in the sputtering chamber and the target's performance.
Plasma Spray and Wire Flame Spray Product Group
Plasma Spray
Plasma Spraying is an extremely versatile thermal coating process. A plasma is produced and controlled through a specially designed torch by excitation of an inert gas passing through an electric arc, creating a very hot ionized gas. Plasma Spraying provides a unique opportunity to mix and blend materials that are otherwise incompatible. Complex alloys, elemental materials, composites and ceramics can often be produced with this technique for use in target material fabrication.
The coating material, in powder form, is injected into the gas stream where it becomes molten and accelerated onto the substrate. Here, layer by layer, a buildup through intraparticle bonding and sintering reaction takes place.
This technology is especially advantageous for rotatable sputtering targets. Plasma sprayed materials can be applied in thickness ranging from this R&D applications to production coating requirements. Our equipment can process materials up to 216" in length. Typical applications are:
Flame Spray
The flame spray process was initially introduced around 1910 in Switzerland by Max Ulrich Schoop. The process included the spraying of ceramics, metals and "metal oxides."
The development of the process was enhanced in the 1950's as the United States applied greater emphasis to space exploration. Many new metal alloys were developed in the hard facing field. Today, flame spraying is a well recognized process implementing wire metals as the coating material. It could be defined as the process of melting materials in a heating zone and accelerating them in a molten state onto a target to form a coating. In the spraying process, the hot particles are quenched, or rapidly cooled, upon hitting the substrate.
The actual atomizing and propelling of the coating particles is accomplished by a surrounding stream of compressed gas.
Process Materials Inc., has extensive R&D capabilities and maintains one of the industries most complete spraying and production facilities available. Through precise control of spraying parameters, Process Materials obtains an unparalleled level of coating quality and uniformity.
Quality Control
All aspects of material production are rigidly controlled assuring thorough compliance with customer specifications. From incoming raw material to final product, Process Materials adheres to the highest quality standards.
Advanced Grinding Capabilities
Process Materials utilizes numerically controlled equipment to assure the highest degree of accuracy and precision on finished dimensions. Our facility maintains the most modern and complete grinding capability to satisfy the most demanding applications.
Precision Machining Support
Process Materials provides complete precision machined capabilities. Process Materials can machine the most sophisticated parts for coating and finishing. At Process Materials, we possess a complete facility for plasma spraying and flame spraying (metalizing) to service your coatings to gain durability and utilization advantages. Contact Process Materials to discuss your material requirements today.